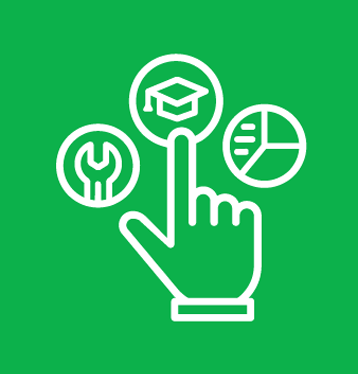
Service
We believe in the closing loop. By servicing organic waste treatment plants worldwide, we can focus on what’s really important: continuous improvement and optimization. Together with our clients we innovate and then implement organic waste management solutions that make a difference.
Continuous
improvement
is our promise.
We specialize in creating loops onsite to maximize output and minimize operational expenditures.
Our Solutions
To manage an organic waste treatment facility, you need to be able to adapt to changing conditions. Waste composition, gate fees, personnel, equipment wear and regulations can all dramatically change a site’s business model.
We are proud to provide high-level servicing support at more than 50 facilities worldwide. Based on the needs and goals of our clients, we create effective solutions for all kinds of organic waste treatment techniques and odour abatement solutions. These range from single annual inspection visits to daily tilling and 24/7 remote support.
WE OFFER A VARIETY OF SERVICES
Helpdesk & Emergency Support
If problems arise, our team of PLC and SCADA specialists are available 24/7. They’ll provide the right support to make sure your facility is up and running as soon as possible. We can even complete and/or supervise on-site work.
Plant Audits & Inspections
Make sure your waste management operation is safe, profitable and long-lasting. Our Service team will perform an in-depth review of your waste processing equipment to determine;
- General condition
- Required maintenance
- Potential
- Current state of safety
When the audit is complete, we share our findings with a report outlining our findings and recommendations for potential improvements.
Remote Monitoring Reports
From our Control Room, our team of experienced Process Technologists monitor your waste management plant’s performance 24/7. Our specialists analyze your process data and spot trends, to help you optimize your operations.
Process Optimization
An efficient biological process is essential when trying to maximize your compost quality or biogas production. We are always proactive by adding new process recipes or updating existing parameters as required. These improvements are performed under the direct control and supervision of our waste processing specialists.
Training
We are enthusiastic about sharing knowledge. Every waste treatment plant and waste stream composition is unique. We visit facilities worldwide and train new and existing operators to improve their level of know-how. Most training sessions consist of a theoretical and practical section and end with an exam. Operators receive a certificate for the successful completion of the training.
Spare Parts
We have the technical expertise to put together emergency packages of spare parts for your waste processing facility. We’ve built great relationships with our suppliers, so we can offer quick access to packages and individual parts at attractive prices. These include spare parts for biological and mechanical treatment facilities. With the help of our integrated procurement system, we can manage our clients’ spare parts logistics and requests on time.
Upgrades
Our knowledge centre is unique in the market of Organic Waste Treatment. We are always working on potential improvements to increase a plant’s performance. Recent developments include
Cleaning In Place
A solution to remove scaling from water pipes in Anaerobic Digestion facilities, includes a prefabricated skid with IBC’s and instrumentation.
Water Treatment Module
A solution to purify water on-site and avoid disposal costs to a Wastewater Treatment Plant, while complying with acceptable disposal standards regarding sewage or surface waters.
Process Upgrade Package
A series of instrumentation and monitoring methods to help you upgrade and monitor the process in a better way and avoid changing improper outputs.
View Past Client Projects